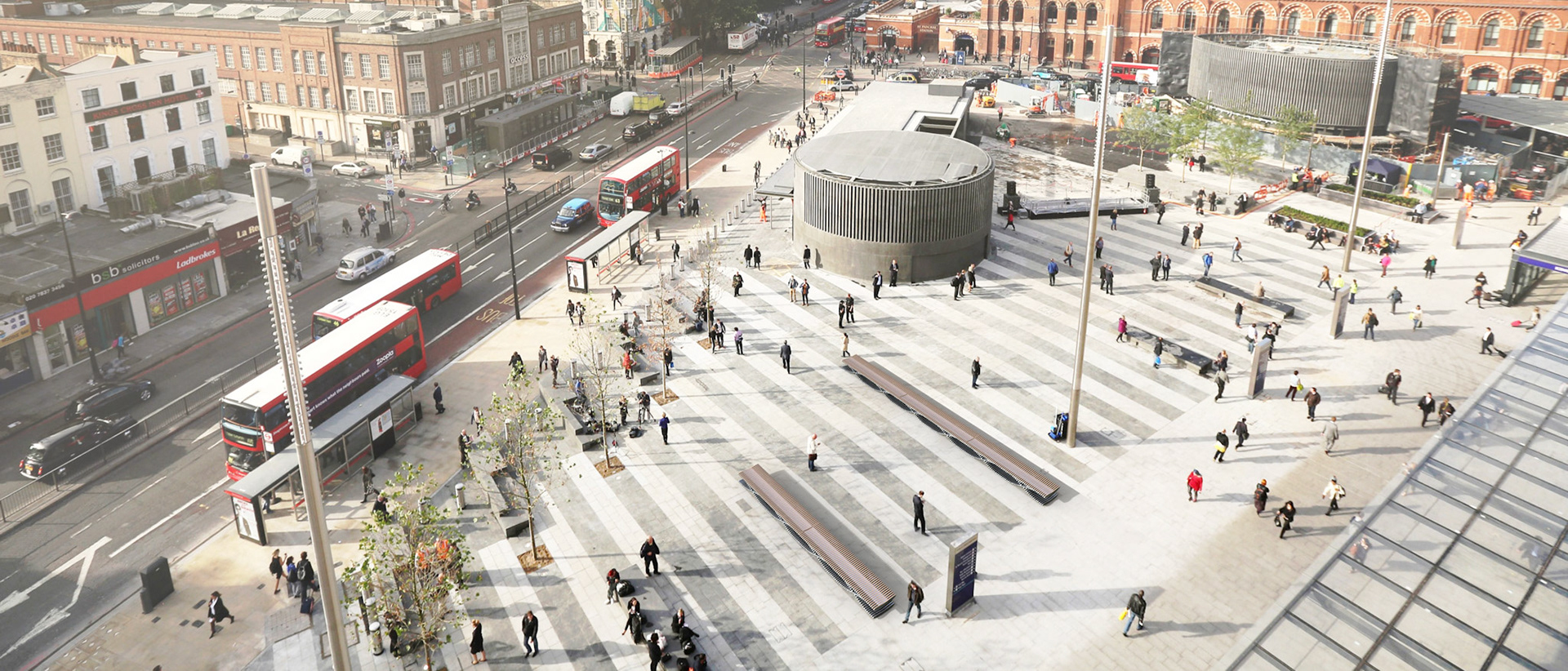
London faces an increasing pollution problem. Commuters and travellers frequenting busy roads are being subjected to unhealthy amounts of pollutants including nitrogen dioxide. This is leading to decrease in health and the loss of life.

In response to this issue I designed an air cleaning bench that uses a titanium dioxide coating on its aluminum shell to convert nitrogen dioxide, created by traffic, into non harmful compounds. The bench has a compact footprint and a scalable design in order for it to be placed in areas as necessary. Each bench is capable of reducing ‘smog’ with a capacity comparable to that of two trees. Five units of Altion, positioned at Kings Cross station, could thus clean as much air as ten trees.
This project was a LVMH Greentrail Award Finalist at the Central Saint Martins degree show 2018. Spanning various design disciplines this award was given to outstanding projects which demonstrate sustainable innovation.
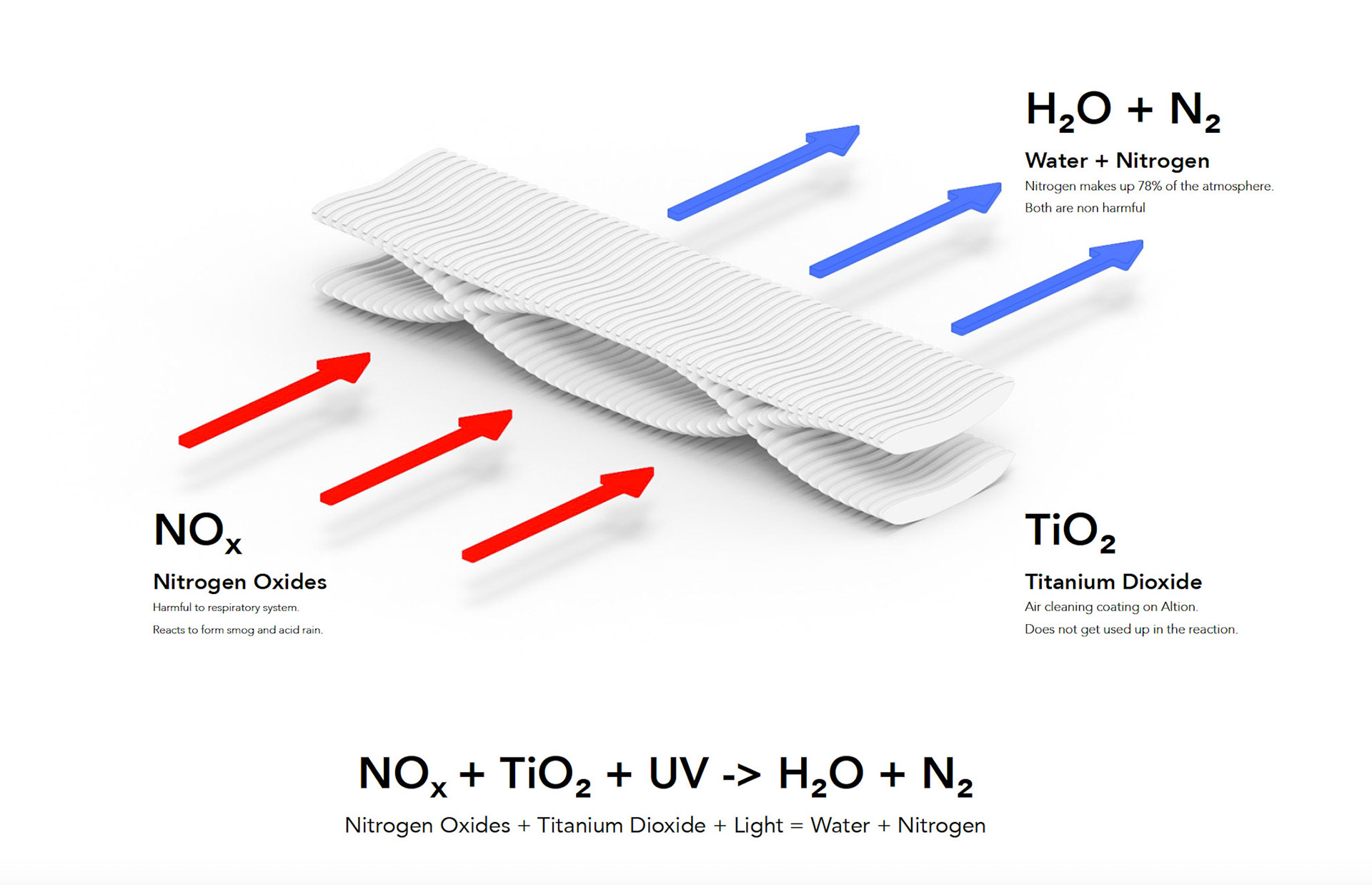
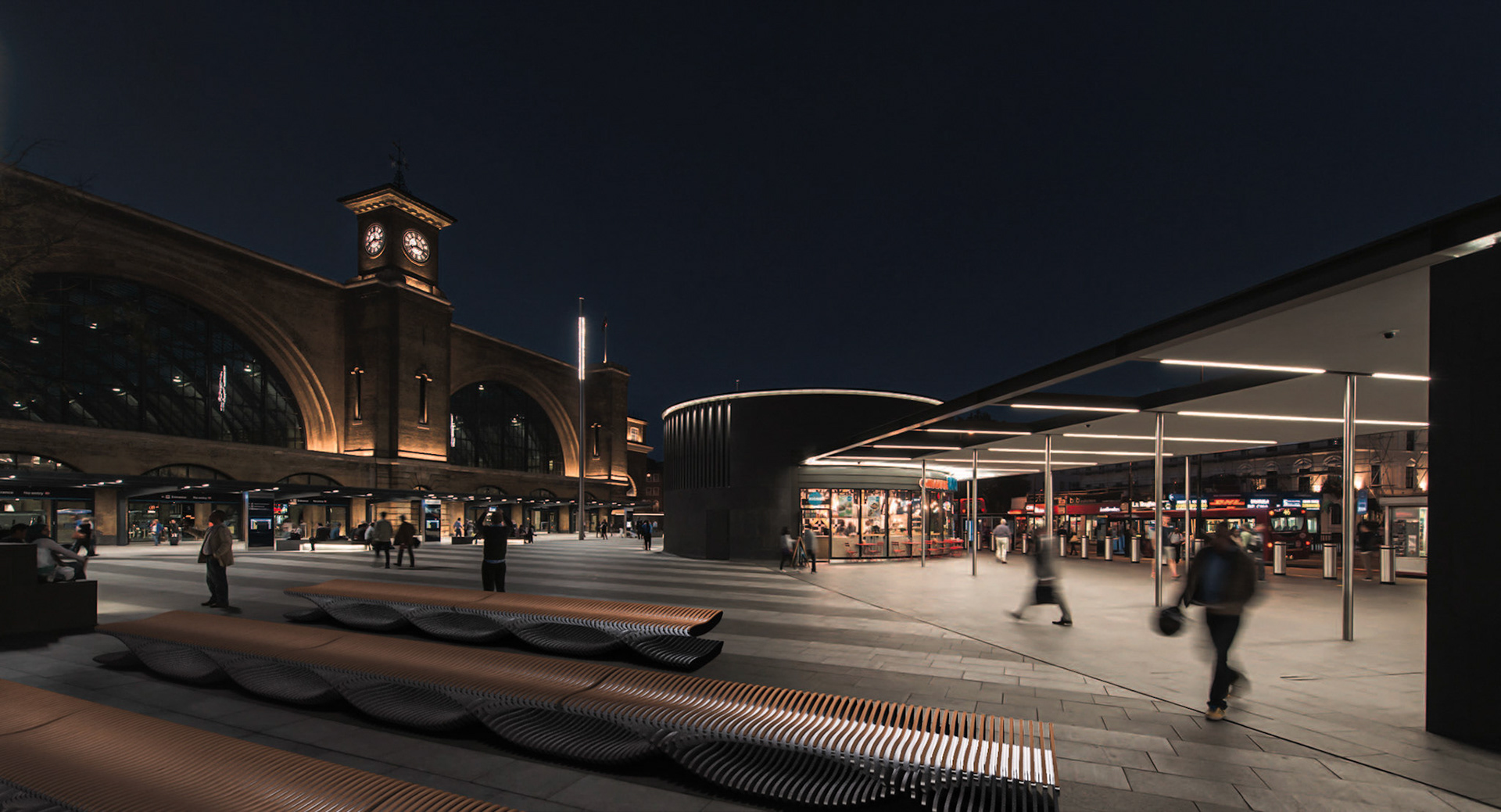
Altion’s helix inspired silhouette not only echoes its biological function but also helps the product scale seamlessly in applications where more than one unit is used. This can be observed in the image on the left which shows how various units can be used together. The sectioned design in combination with the light source is driven by the fact that this kind of arrangement has more surface area. More surface area coated with air cleaning titanium dioxide, means that more nitrogen dioxide can be converted.
The light fixtures between every section not only aid ambient lighting at night but also have the purpose of accelerating the air cleaning reaction when natural light is low. The coating, as the catalyst, does not get used up by the reaction with light. It is also hydrophilic, making the otherwise difficult to clean sections easily washable. When worn down the wooden seat covers on each section of the bench can also easily be replaced thus extending the life expectancy of the rest of Altion.
A video summarising my research findings can be seen below.
The Models
In order to present the design, I made a scale, as well as full size section, model. The process images show how I used digital manufacturing techniques ranging from laser cutting, cnc machining and 3D printing, alongside analogue manufacturing processes to create the final model.
The cross section model gives insight into the construction and joinery within the bench. The steel subframe structure as well as the inside of the LED light fixtures between the aluminium sections of the bench become visible. The honeycomb structure comprising the core of the aluminium sections can also be seen.
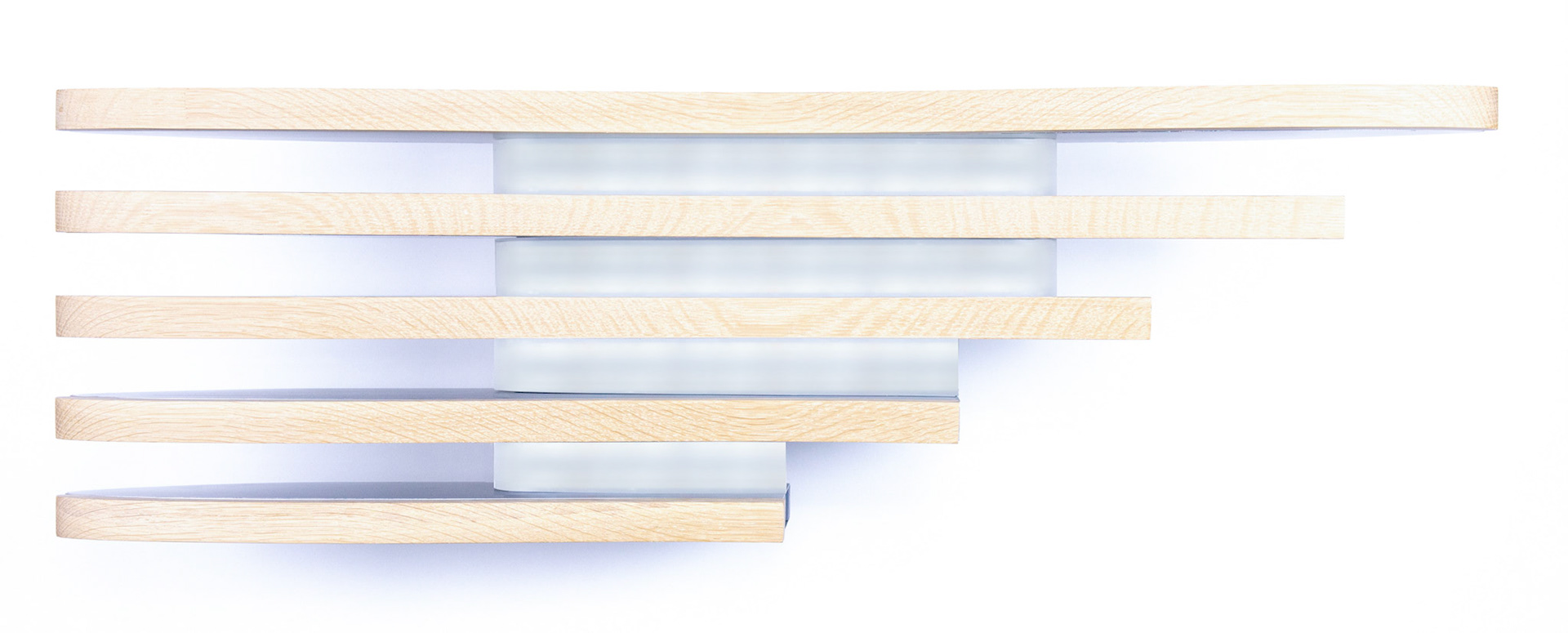
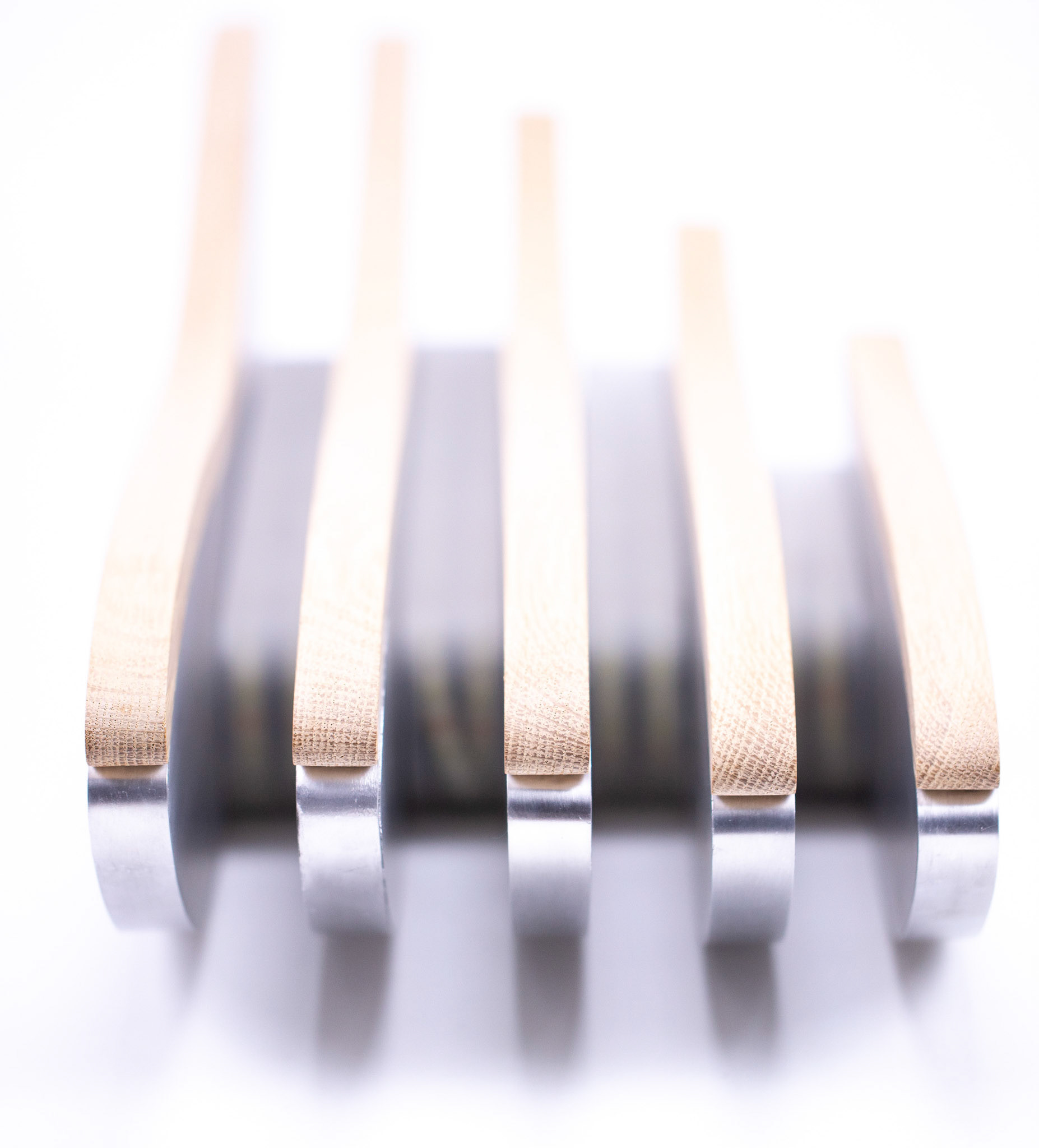
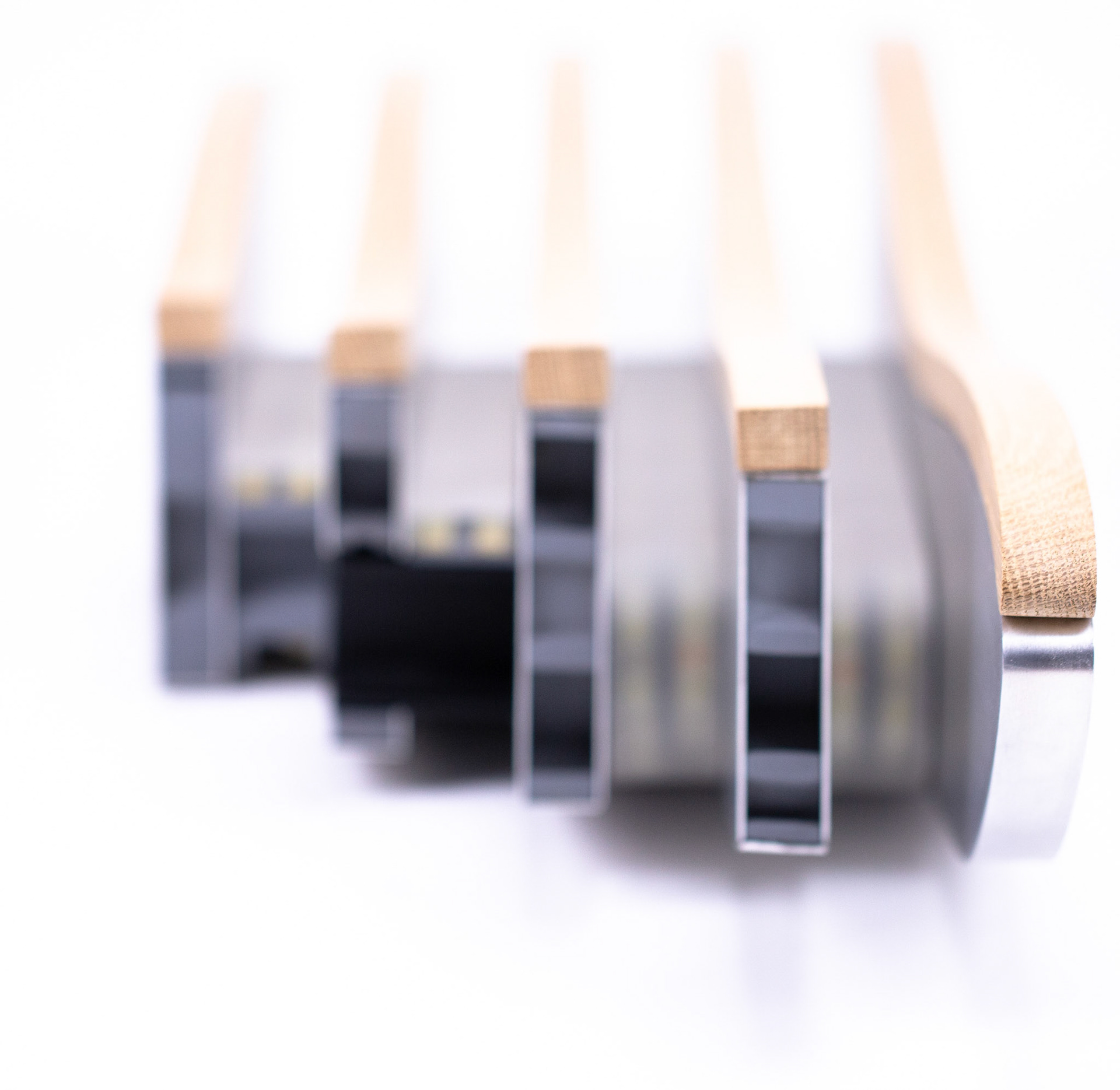
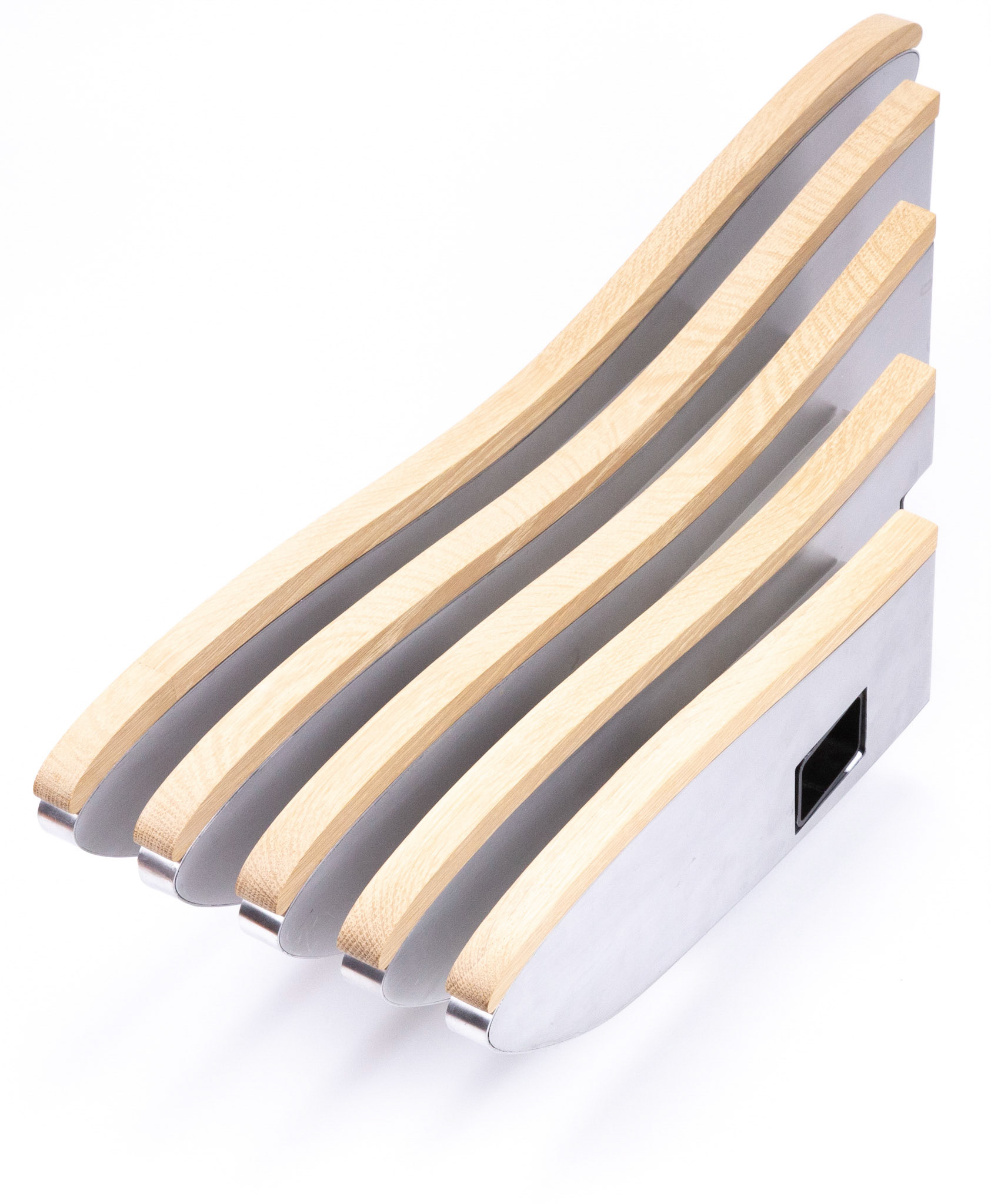
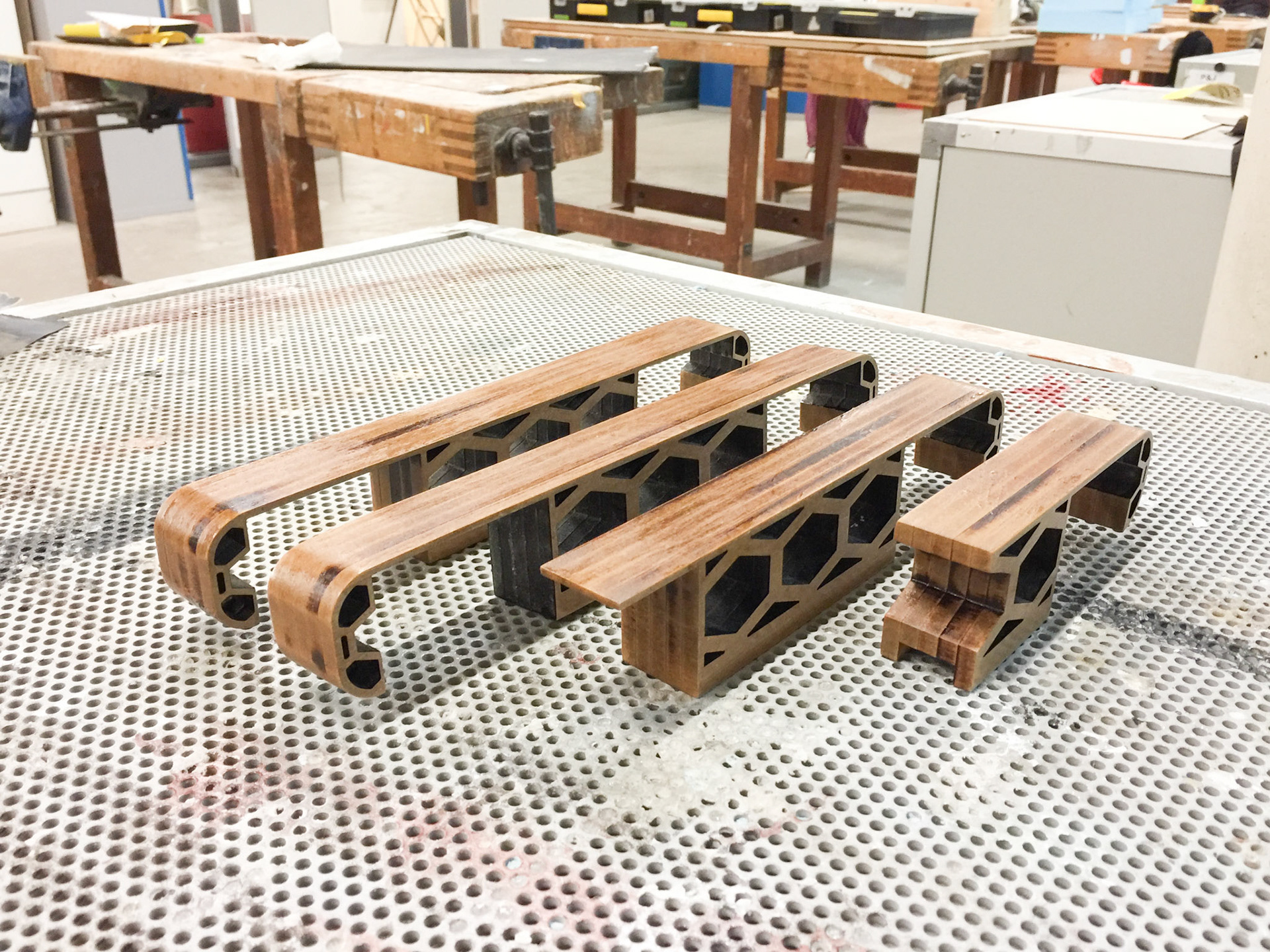
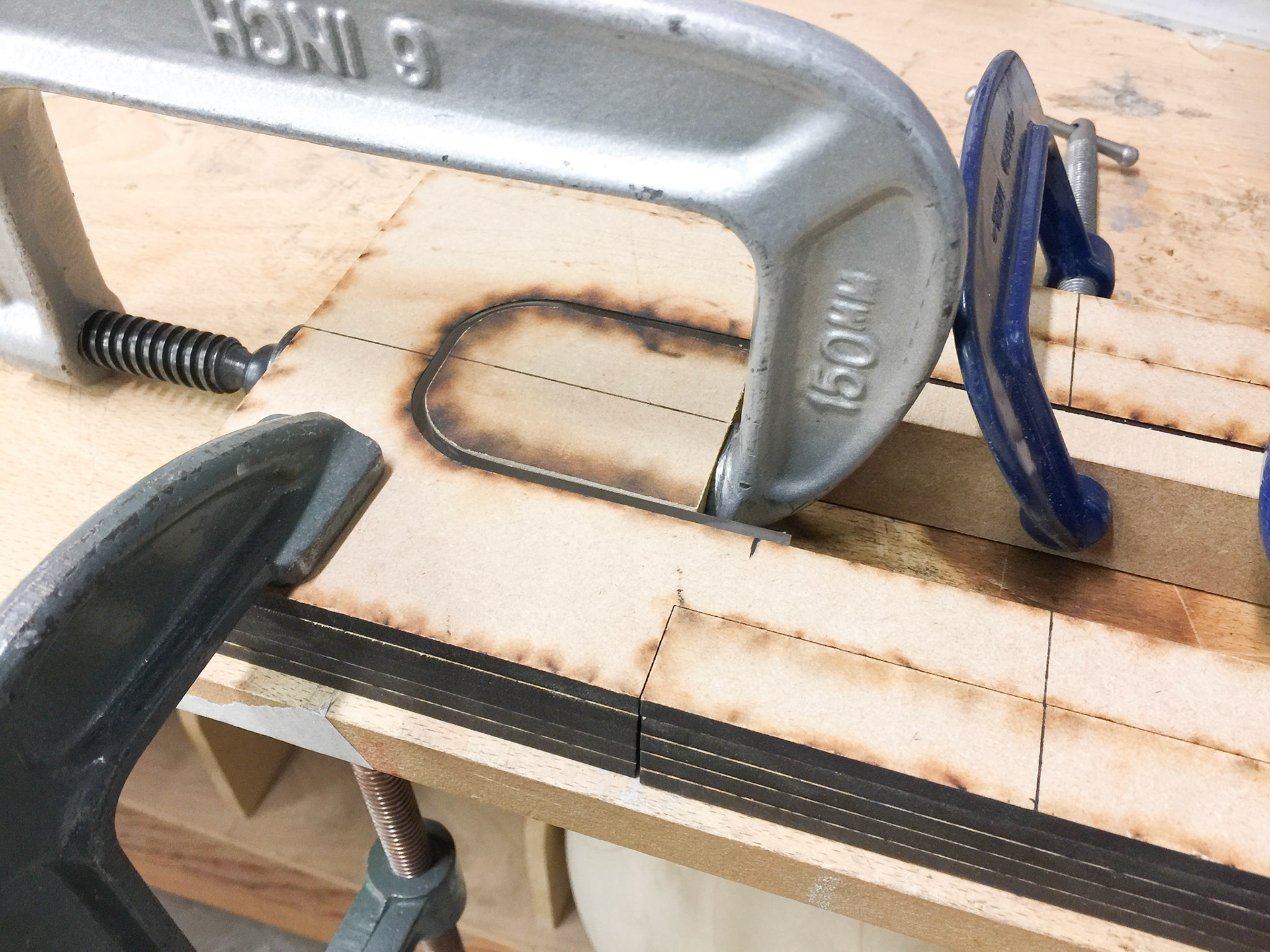
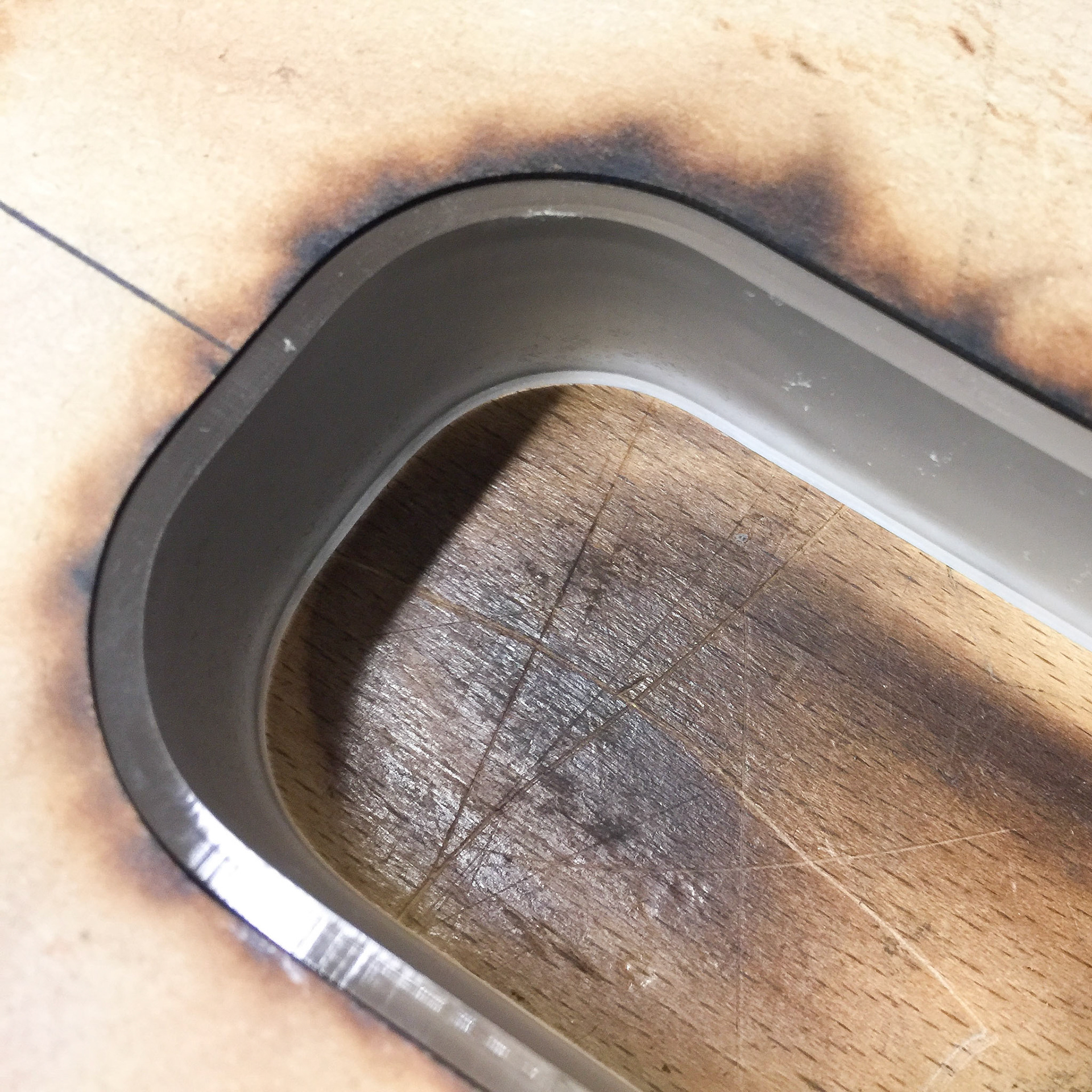
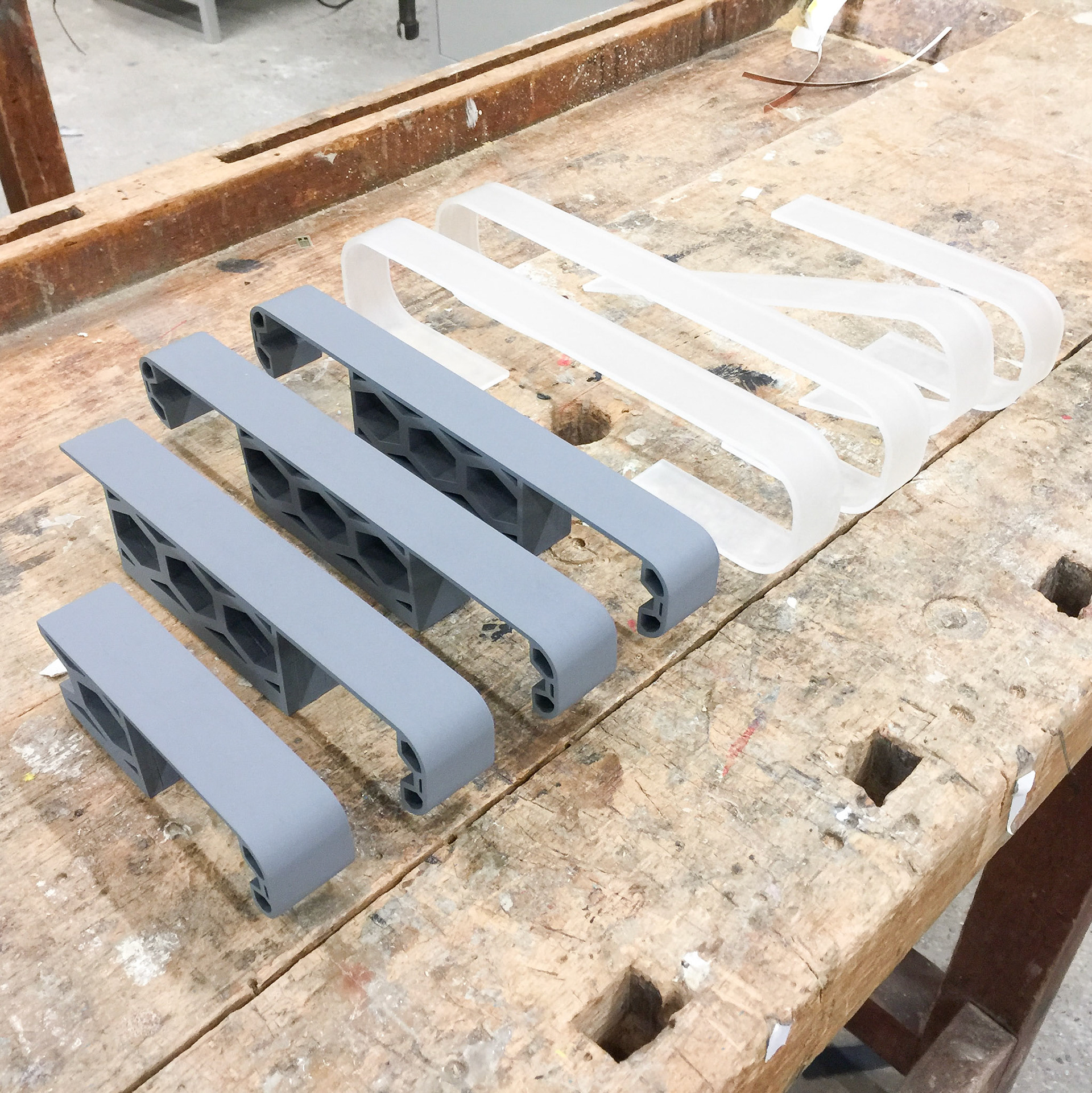
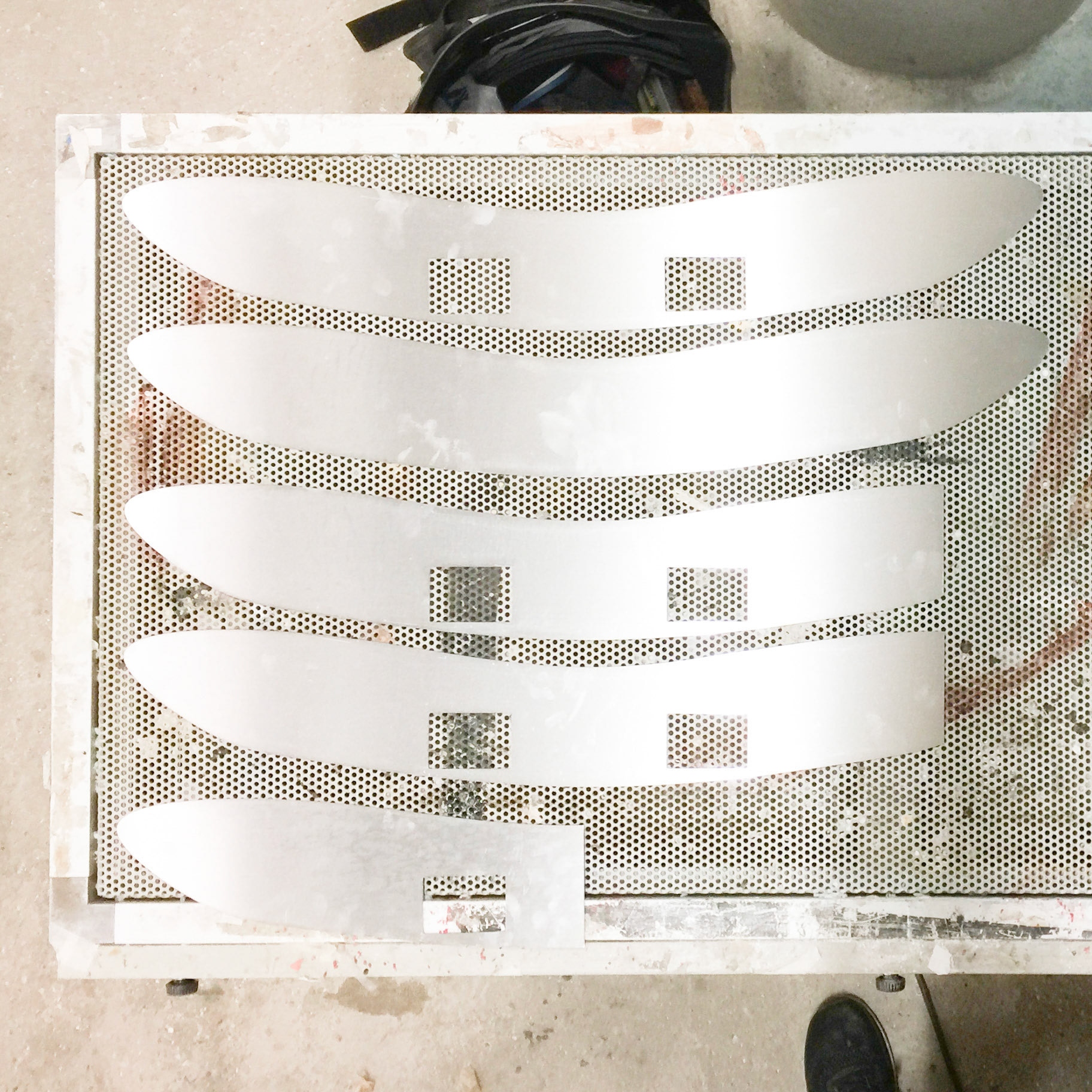
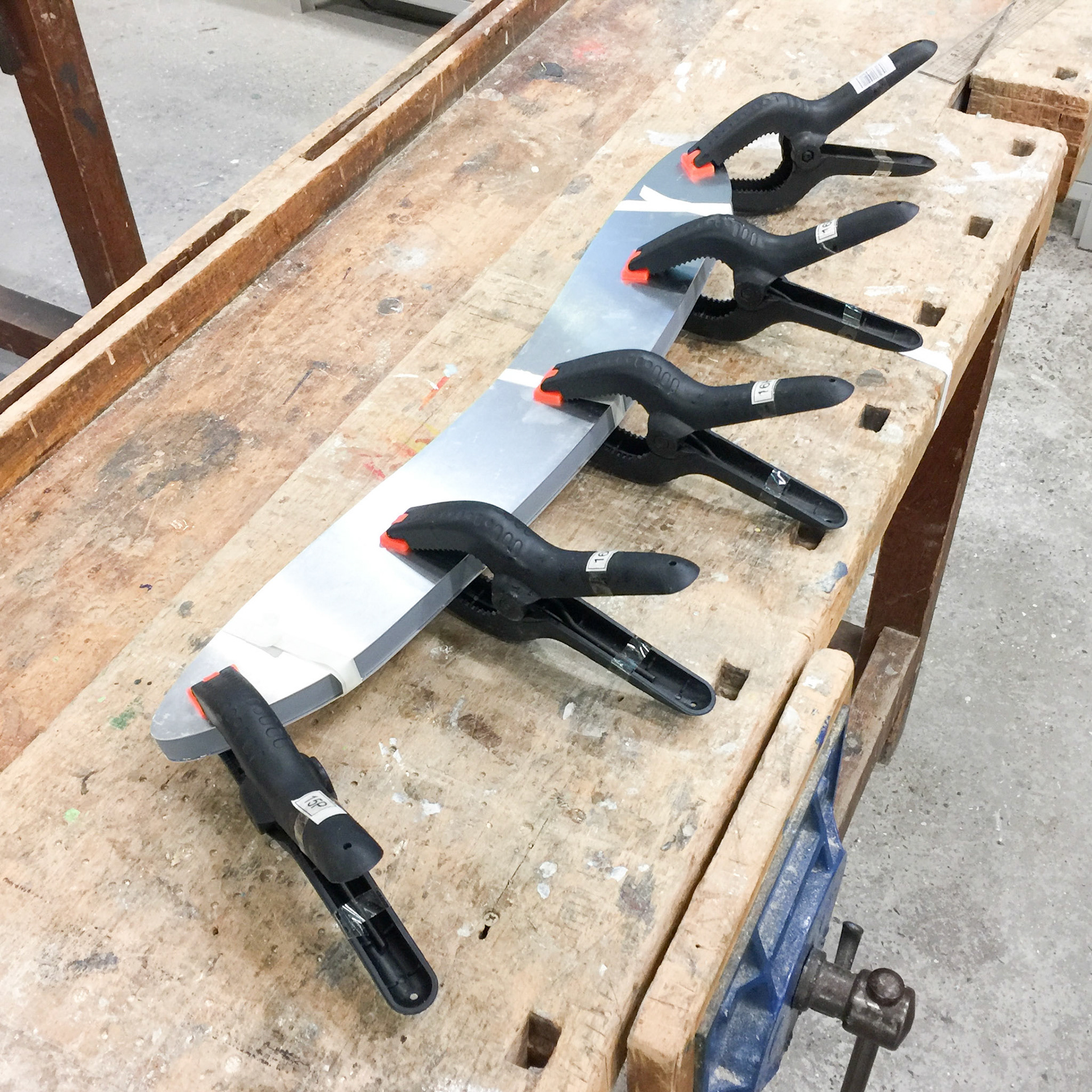
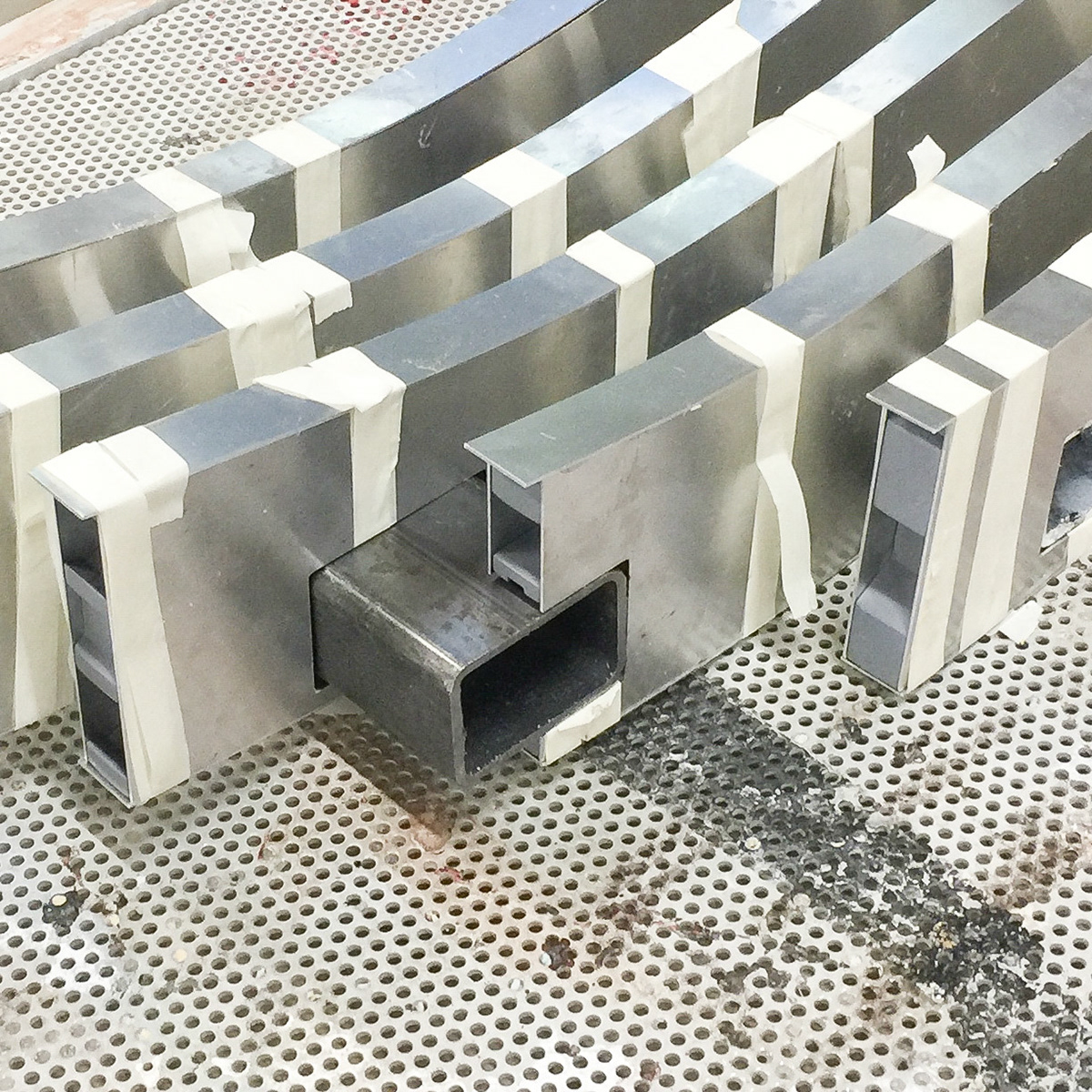
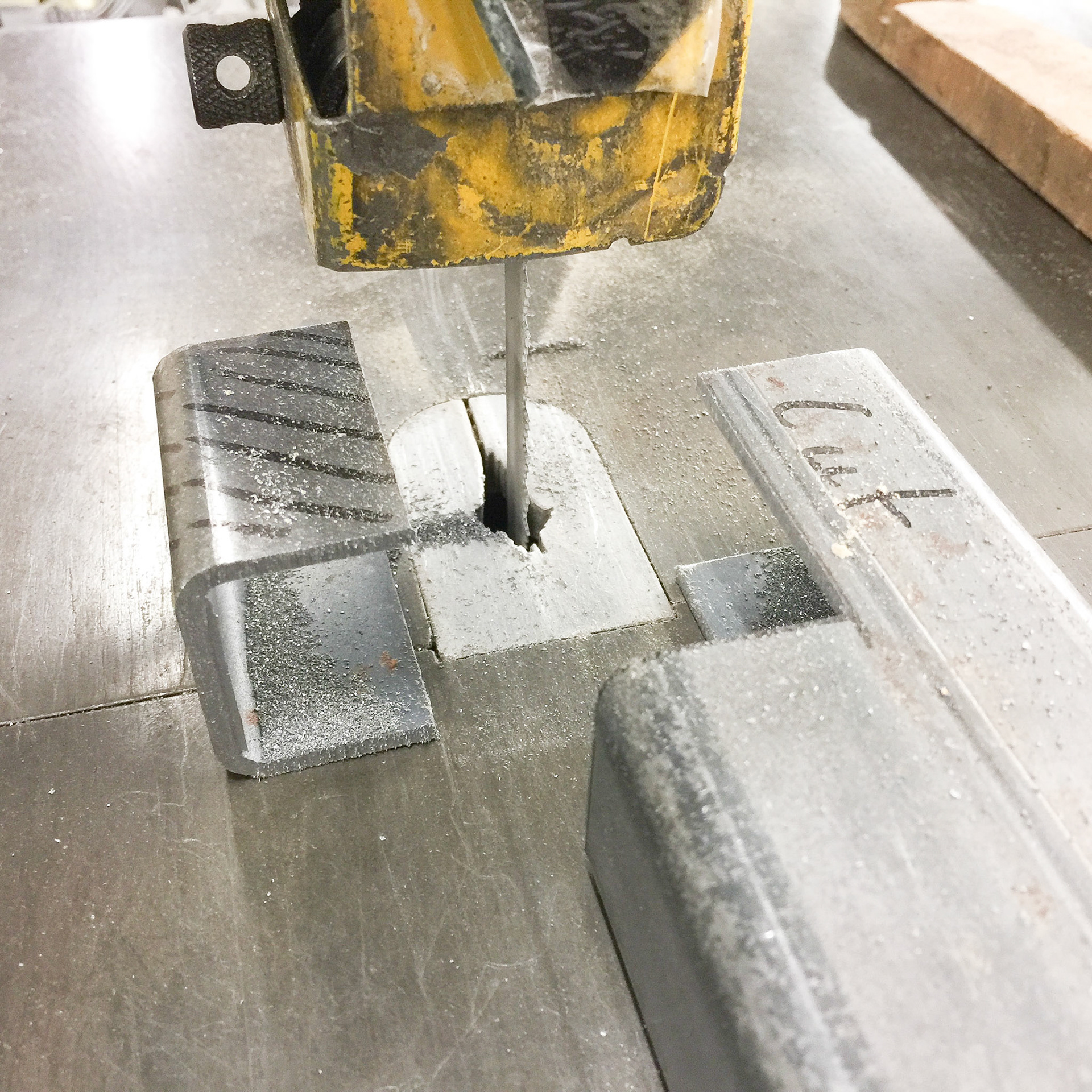
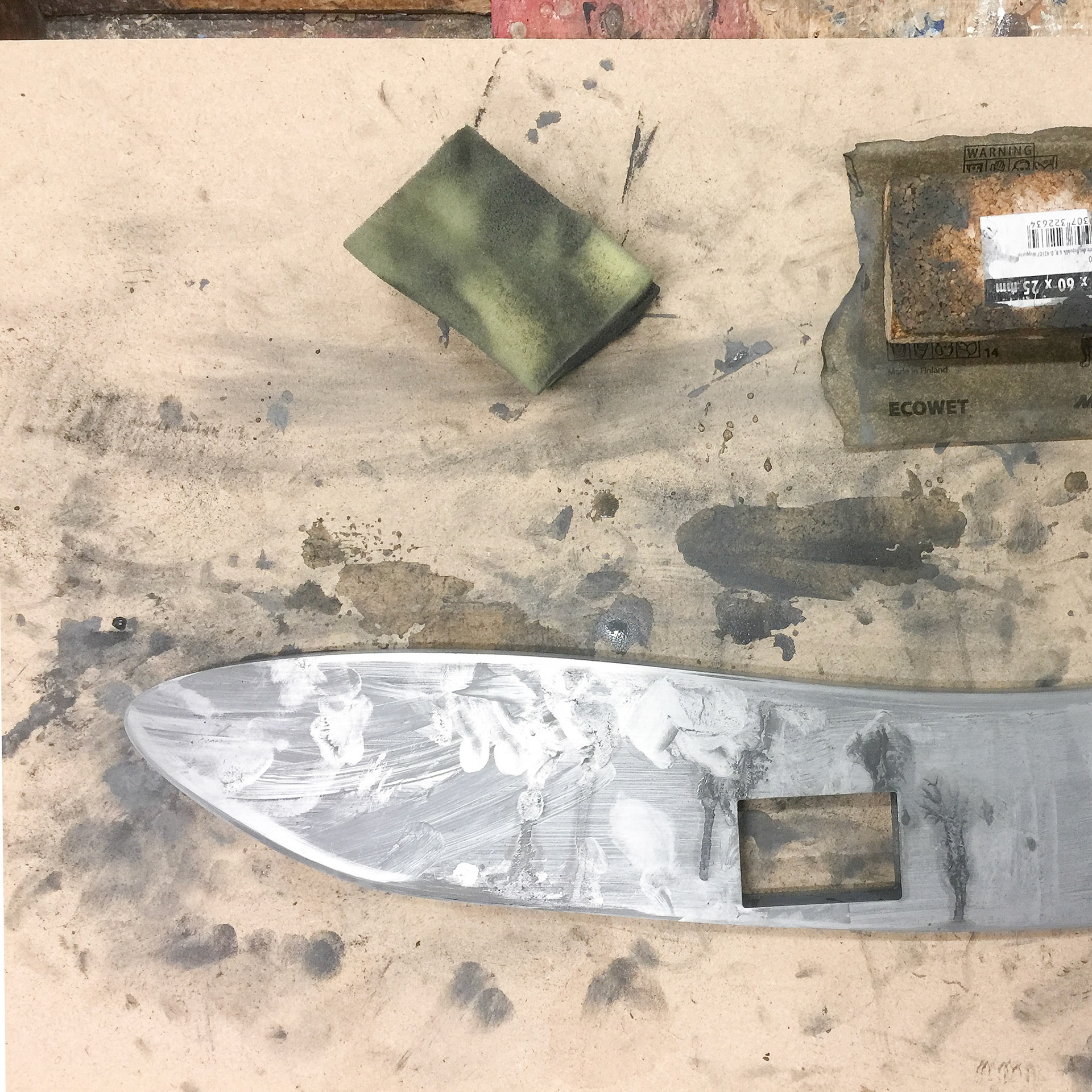
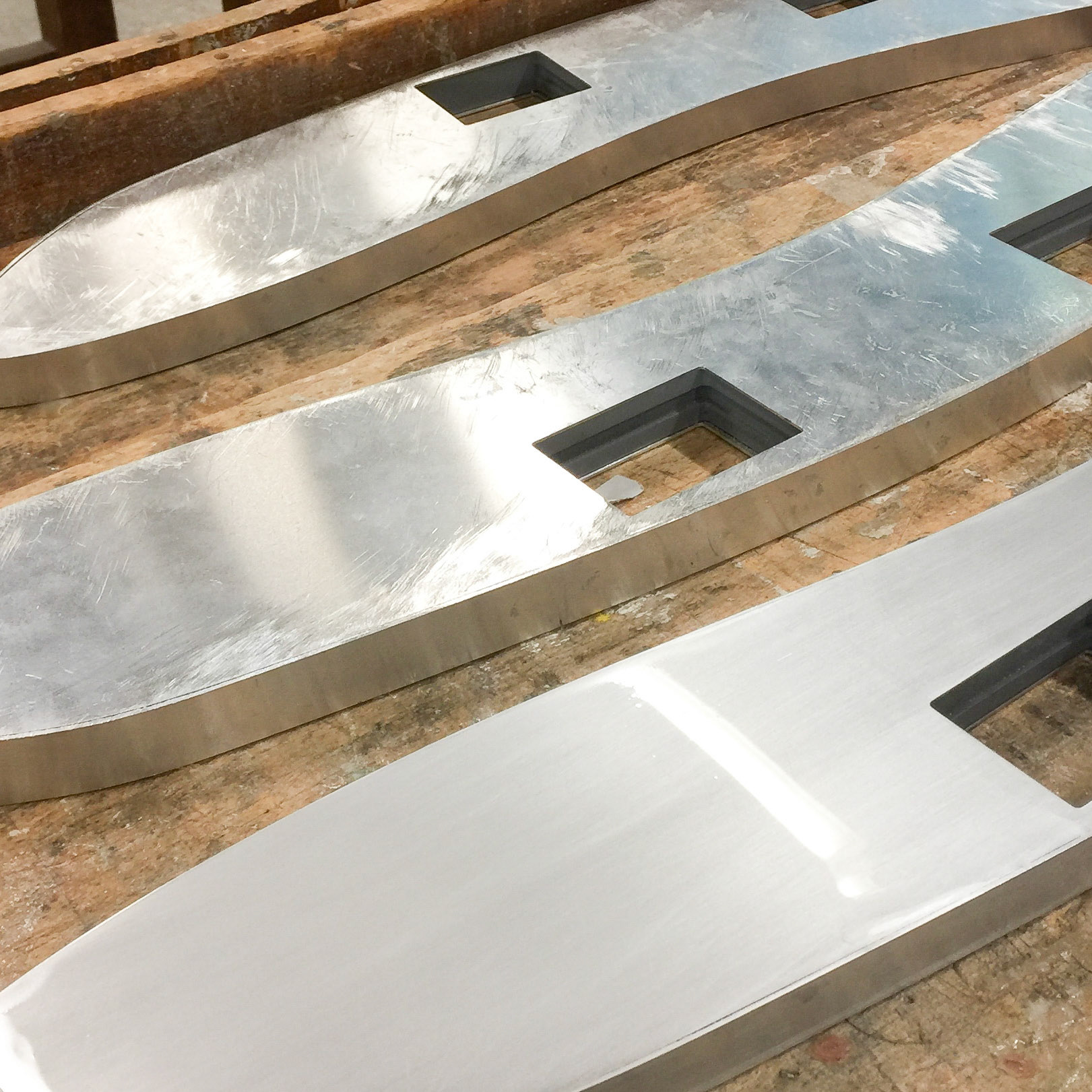
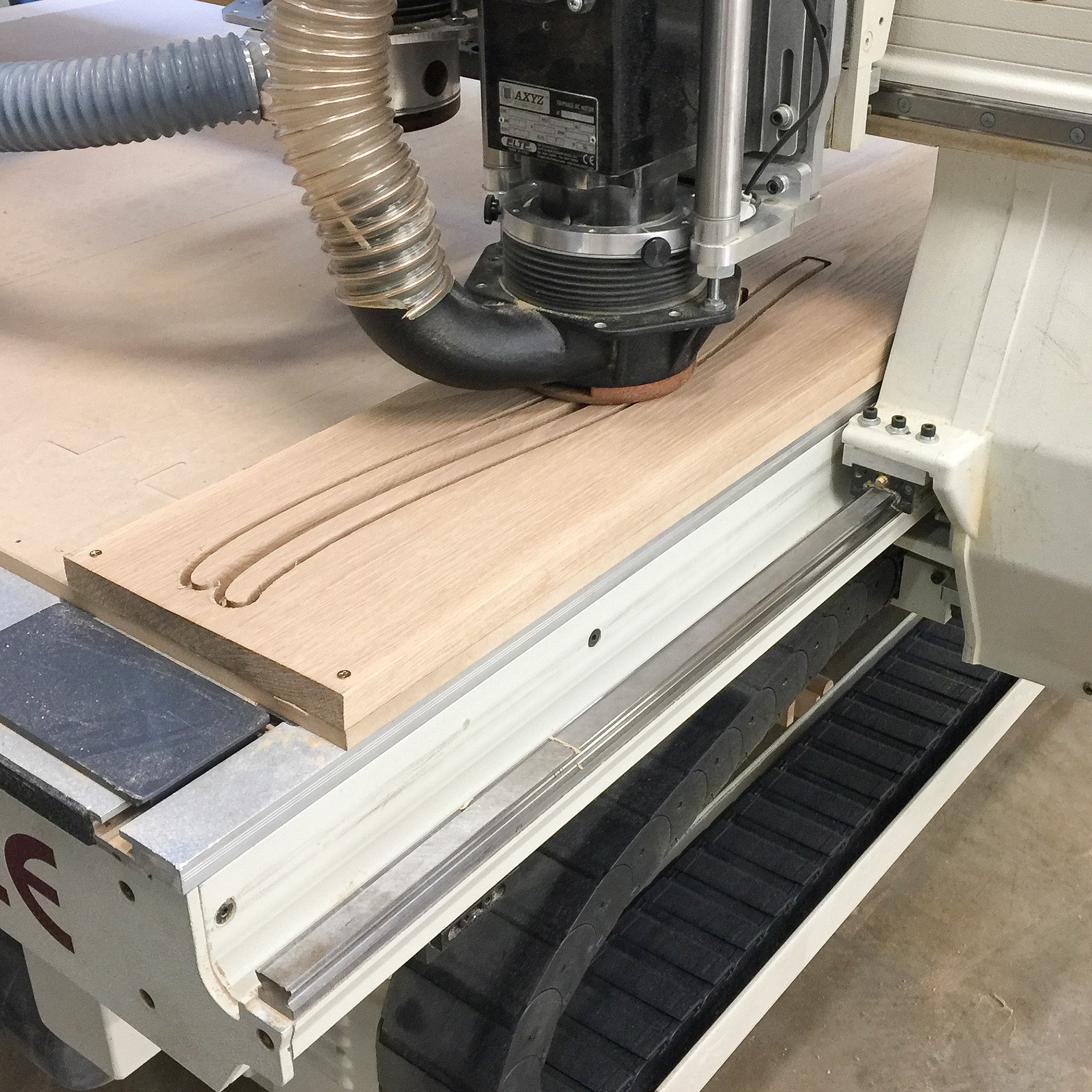
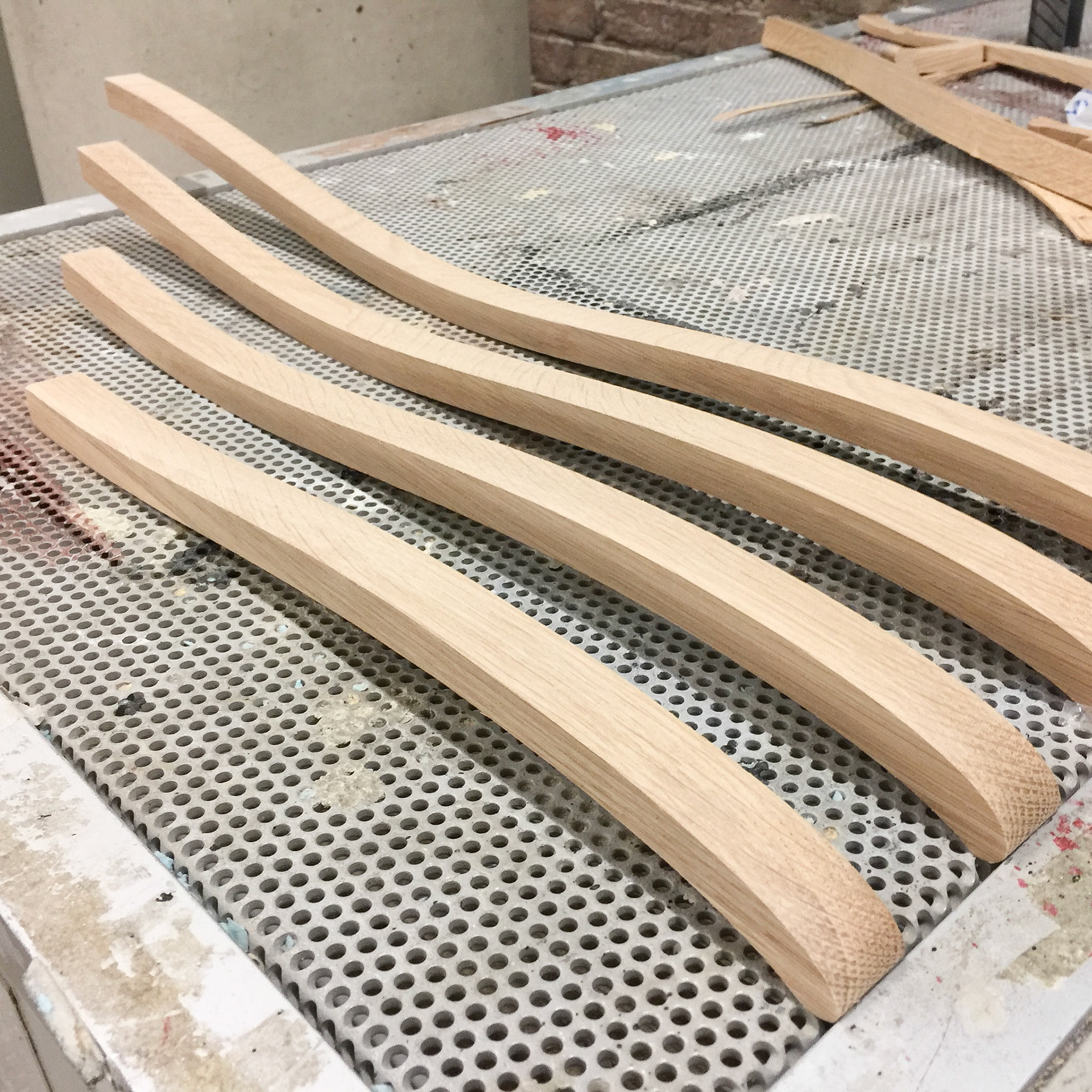